In a serious development for metallic additive manufacturing, researchers at Lawrence Livermore Nationwide Laboratory (LLNL) and their tutorial companions have developed a brand new methodology that considerably enhances the optical absorptivity of metallic powders utilized in 3D printing. This breakthrough might result in extra environment friendly and higher-quality manufacturing of metallic components, particularly for difficult supplies like copper and tungsten.
Addressing Challenges in Steel Additive Manufacturing
Steel 3D printing, significantly laser powder-bed fusion (LPBF), has remodeled the manufacturing panorama by enabling the manufacturing of advanced and customised parts that conventional strategies usually wrestle to attain. Nevertheless, one ongoing problem is the excessive reflectivity of sure metals, reminiscent of copper, which might hinder power absorption in the course of the printing course of. This inefficiency not solely impacts print high quality but additionally will increase power consumption, resulting in greater operational prices and potential machine harm.
To sort out this problem, a staff of scientists from LLNL, Stanford College, and the College of Pennsylvania launched an progressive strategy known as moist chemical etching. This system modifies the floor of metallic powders by creating nanoscale textures, permitting them to soak up extra power in the course of the laser-melting course of. The examine, printed in Science Advances, studies that this methodology has elevated the absorptivity of metallic powders by as much as 70%.
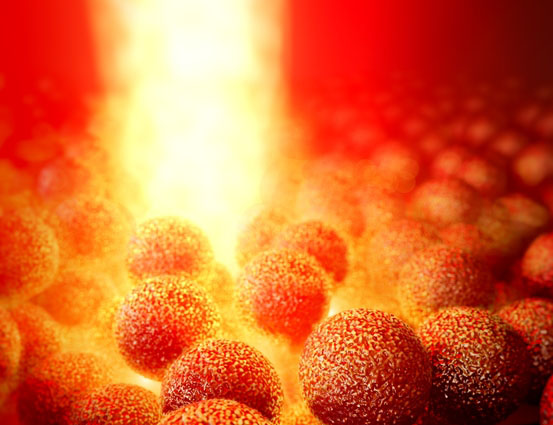
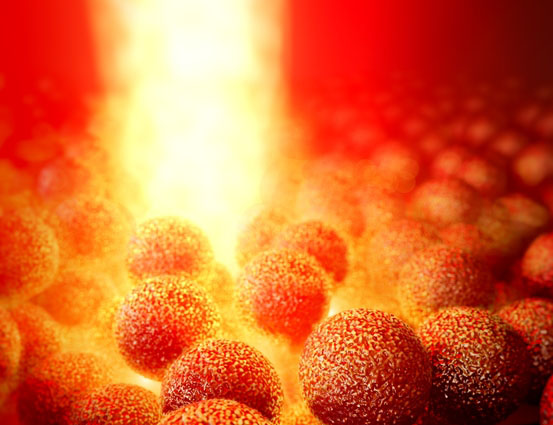
The Moist-Etching Course of and Its Influence
The method includes immersing metallic powders, reminiscent of copper and tungsten, in a specifically formulated resolution that selectively removes materials from the floor. This ends in the formation of nanoscale grooves and textures, enhancing the powder’s capability to soak up laser gentle. The staff used superior imaging strategies like synchrotron x-ray nanotomography to visualise the floor options of the powders and precisely mannequin how these modifications affect power switch throughout 3D printing.
The improved absorptivity permits for extra environment friendly power utilization throughout printing, which is very useful for supplies like copper which might be historically troublesome to work with. “Our methodology enhances the absorptivity of copper with out compromising its fascinating properties, reminiscent of excessive thermal and electrical conductivity,” stated Philip DePond, co-lead creator and LLNL supplies scientist. “We demonstrated that laser-powder interactions prolong past the soften pool, which might be advantageous for the printing course of.”
Effectivity Features and Sustainable Manufacturing
The improved absorptivity of metallic powders is a major step towards decreasing power consumption in manufacturing. The researchers discovered that by utilizing much less power, they may print high-purity copper and tungsten parts with relative densities of as much as 99%. This not solely improves the standard of printed components but additionally minimizes the environmental affect of the manufacturing course of by decreasing the power required for manufacturing.
For instance, the staff was capable of print copper buildings utilizing lower than 100 J/mm³ of power, a spread usually used for supplies like titanium and stainless-steel. Tungsten, which normally requires excessive power enter, was printed utilizing about 700 J/mm³, one-third much less power than conventional strategies.
“This breakthrough opens up new potentialities for industries to print copper while not having costly, custom-built machines,” defined DePond. “It lowers the barrier of entry for producers, making metallic additive manufacturing extra accessible and cost-effective.”
Broad Implications for Trade
The power to print with decreased power and better precision might have a right away affect on varied industries. Based on Dan Flowers, chief of LLNL’s Vitality Safety Program, this methodology may benefit purposes starting from warmth exchangers to wash power applied sciences. “Environment friendly printing of copper can assist the event of decarbonization applied sciences and advance our low-carbon power mission,” Flowers famous.
Trying forward, the researchers are curious about exploring how this method might enhance the blending of powders with completely different power necessities for melting. Additionally they plan to proceed optimizing the method to allow the manufacturing of much more advanced and sturdy metallic components.
The brand new wet-etching method marks a serious step ahead within the growth of sustainable and environment friendly metallic 3D printing applied sciences, doubtlessly reworking the way in which industries produce high-performance parts with difficult supplies.
For additional studying you will discover the complete paper titled: “Excessive absorptivity nanotextured powders for additive manufacturing” at science.org.