Hunt Valve, a Fairbanks Morse Protection (FMD) subsidiary, has secured a contract from the Maritime Sustainment Know-how and Innovation Consortium (MSTIC) to fabricate a pioneering 3D printed valve meeting for U.S. Navy submarines.
Using additive manufacturing, the 70-pound valve meeting, a primary for U.S. submarines, guarantees superior high quality and a lowered manufacturing timeline in comparison with conventional sand-casting strategies.
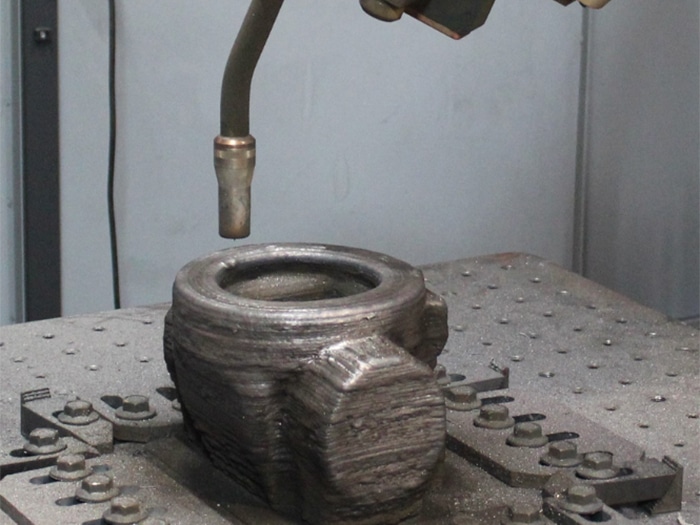
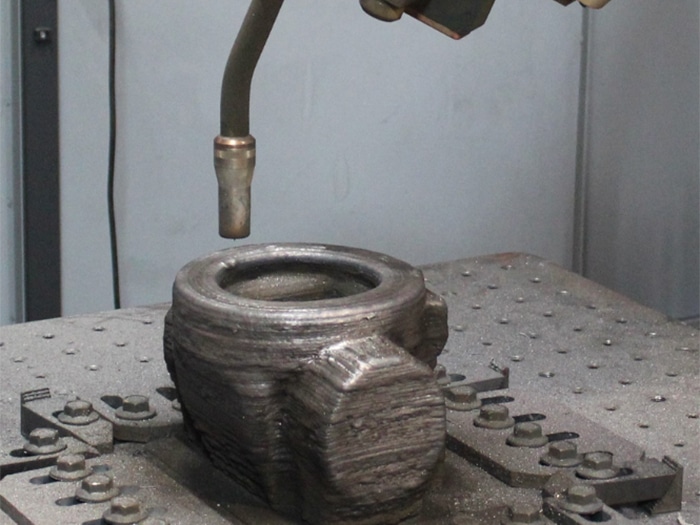
Partnering with Lincoln Electrical, Hunt Valve employs additive manufacturing to craft the valve our bodies, a departure from typical subtractive strategies. By stacking layers of copper-nickel, they obtain heightened effectivity and accuracy, eliminating the challenges posed by porous sand-casted parts.
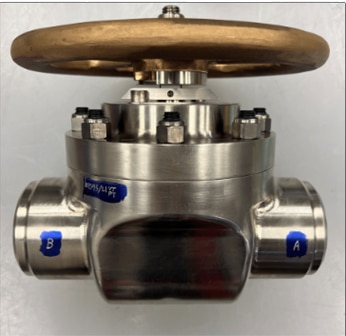
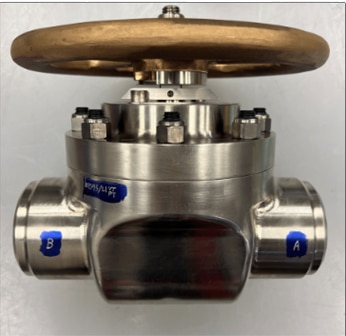
Traditionally, additive manufacturing for submarine elements has been restricted to smaller parts, with purposes for complicated alloys like copper-nickel remaining uncommon. The adoption of 3D printing for valve meeting manufacturing guarantees to speed up Navy fleet part manufacturing by as much as 75%, enhancing manufacturing effectivity and bolstering home provide chain resilience.
“The utilization of additive manufacturing meeting with copper-nickel for big valve manufacturing is an actual step ahead for our trade,” stated Andrew Pfister, vp, aftermarket and product improvement at Fairbanks Morse Protection.
“Not solely does it create a superior product by way of high quality, however the course of can considerably cut back lead-in instances.
Embracing modern applied sciences like additive manufacturing not solely expedites manufacturing but in addition strengthens nationwide safety by decreasing reliance on abroad suppliers.
Come and tell us your ideas on our Fb, X, and LinkedIn pages, and don’t overlook to join our weekly additive manufacturing publication to get all the most recent tales delivered proper to your inbox.