Andaltec, a Spanish analysis heart centered on plastics, has introduced the RECYPPOWDER challenge to discover the chances of recycled polypropylene in additive manufacturing.
Identified for its toughness and light-weight properties, polypropylene is extensively utilized in varied industries for prototyping. Nevertheless, based on the corporate, integrating recycled polypropylene into additive manufacturing processes, significantly SLS, stays comparatively unexplored. Led by Innomaq 21 and in alliance with the College of Barcelona and Andaltec, this analysis goals to develop economical and sustainable supplies appropriate for Selective Laser Sintering (SLS) expertise by leveraging recycled supplies.
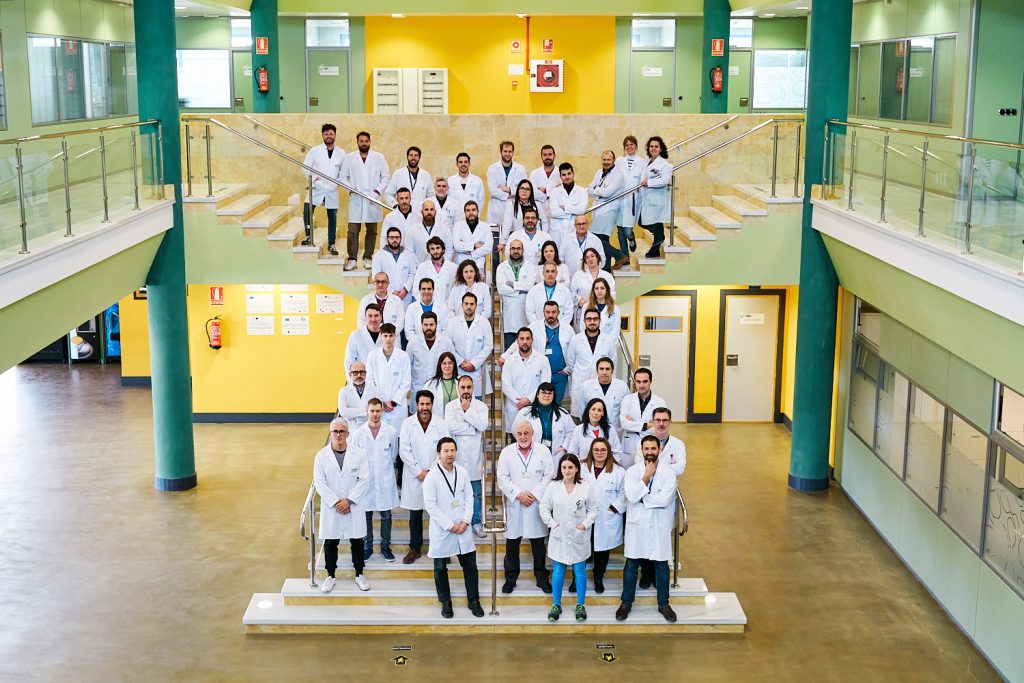
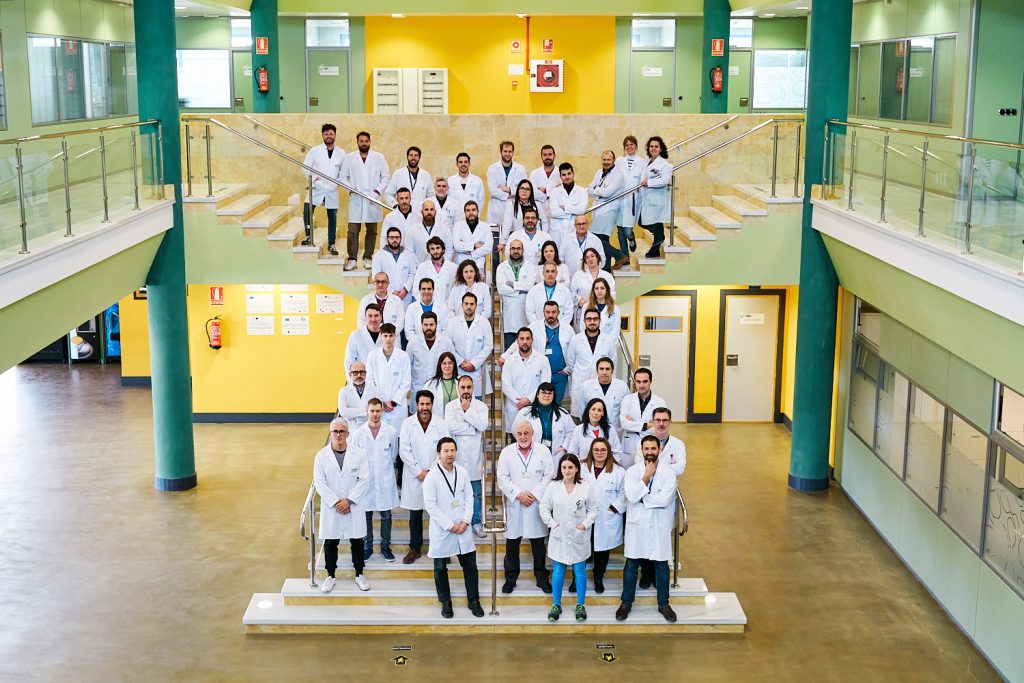
Recycled polypropylene for sustainable SLS 3D printing
In response to the corporate, SLS stands as a flexible 3D printing methodology, famend for its potential to develop extremely exact and complicated elements. Belonging to the powder mattress fusion (PBF) additive manufacturing household, it operates by heating powder inside a container slightly below its fusion level. A curler then spreads a skinny layer onto a producing platform, and a laser selectively sinters the powder, forming an element’s cross-section upon solidification. Subsequently, the platform descends, and the method repeats layer by layer till completion. Upon ending, compressed air cleans the half, whereas the unused powder is collected for reuse, minimizing waste.
Nevertheless, SLS 3D printing faces constraints relating to suitable uncooked supplies. At the moment, polyamide (nylon) is the popular selection, usually enhanced with components like aluminum or glass to enhance last half properties. Nevertheless, there’s a noticeable absence of economic polymer powder derived from recycled polypropylene for SLS functions.
Recognizing this hole, researchers purpose to develop co-polymers mixing industrial and recycled polypropylene, optimizing their particle dimension and properties for laser processing. This entails addressing the inherent variability of recycled supplies in comparison with their virgin counterparts. Furthermore, feasibility research will discover changing half delivery with printing knowledge transmission to cut back carbon footprint.
The challenge’s ambition extends past materials growth, striving to foster a round financial system and sustainability. By testing the novel product on SLS 3D printers below real-world circumstances, the initiative seeks to validate its viability and affect. Andaltec’s involvement encompasses essential duties reminiscent of materials choice, compatibility research, and characterization, highlighting its dedication to advancing additive manufacturing.
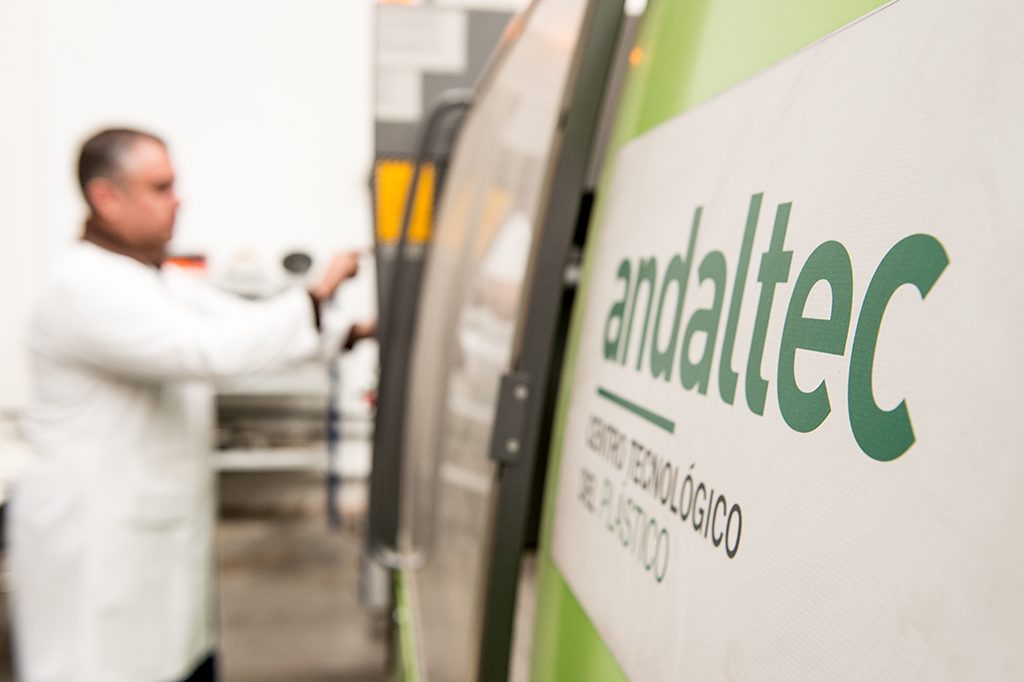
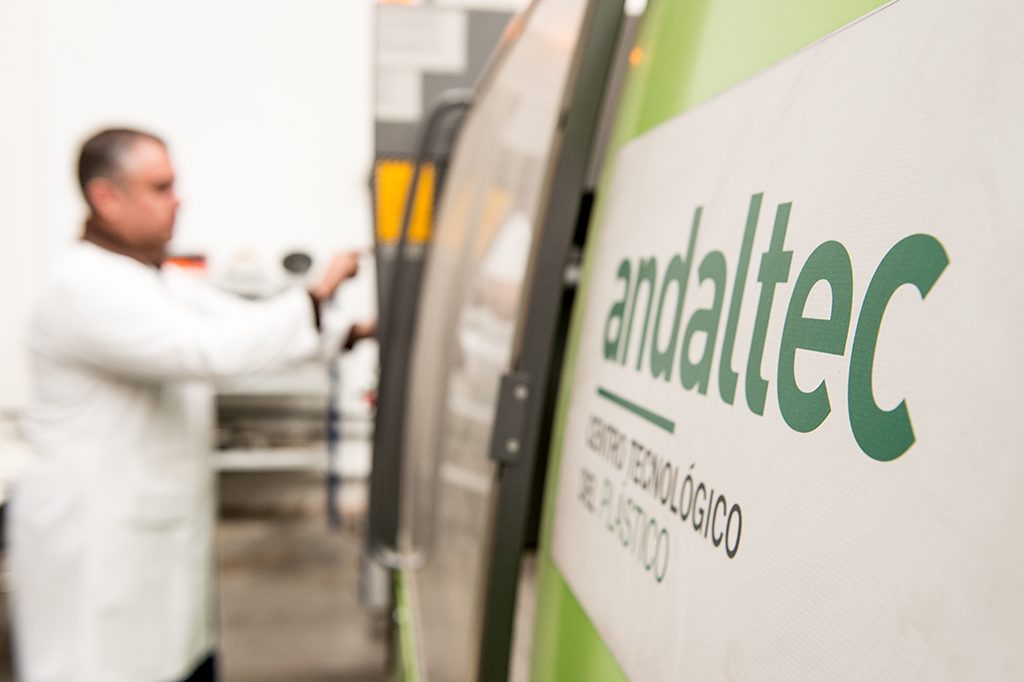
Exploring the unexplored in polypropylene 3D printing
Regardless of its standing as some of the consumed plastics globally, polypropylene has but to succeed in its full potential in 3D printing as a result of inherent challenges. In an interview with 3D Printing Trade, Sebastian Schmidt, Product Supervisor at PPprint, mentioned the underutilization of polypropylene in 3D printing regardless of its widespread use in different industries.
Schmidt highlighted the challenges surrounding interlayer bonding and warping which have hindered PP’s full potential in additive manufacturing. Nevertheless, PPprint, specializing in polypropylene 3D printing supplies, goals to vary this narrative. With a devoted give attention to polypropylene for over 4 years, the corporate has developed an in depth supplies portfolio and affords specialised printing providers to beat these challenges and speed up polypropylene adoption in varied sectors.
On one other entrance, Braskem and Titan Robotics collaborated to unveil a brand new polypropylene resin for Titan’s Atlas 3D printers, focusing on large-format manufacturing elements. The partnership addressed challenges in printing with polypropylene, leveraging its recyclability and strong properties.
After intensive analysis and growth, the companions launched a photopolymer optimized for large-scale polypropylene 3D printing, boasting low warping and robust inter-layer adhesion. This consequently would increase polypropylene’s utility potential within the automotive, packaging, and industrial sectors.
What 3D printing traits do the business leaders anticipate this 12 months?
What does the Way forward for 3D printing maintain for the subsequent 10 years?
To remain updated with the most recent 3D printing information, don’t neglect to subscribe to the 3D Printing Trade e-newsletter or comply with us on Twitter, or like our web page on Fb.
When you’re right here, why not subscribe to our Youtube channel? That includes dialogue, debriefs, video shorts, and webinar replays.
Are you in search of a job within the additive manufacturing business? Go to 3D Printing Jobs for a collection of roles within the business.
Featured picture reveals Andaltec’s group. Picture through Andaltec.