Senior Airman Devon Phrase from the U.S. Air Power’s forty eighth Munitions Squadron has developed a 3D-printed insert to deal with a longstanding concern with 20 mm ammunition jamming in the course of the loading course of. The innovation, used at RAF Lakenheath, U.Okay., enhances the operation of the Common Ammunition Loading System (UALS) by resolving a design flaw within the replenisher desk, the place rounds would continuously jam, inflicting delays and risking damage.
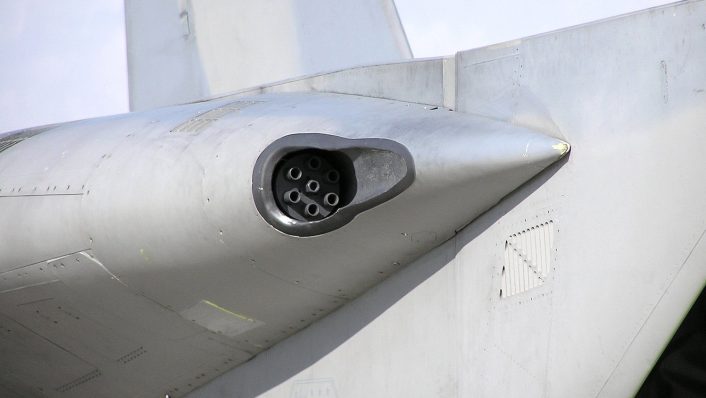
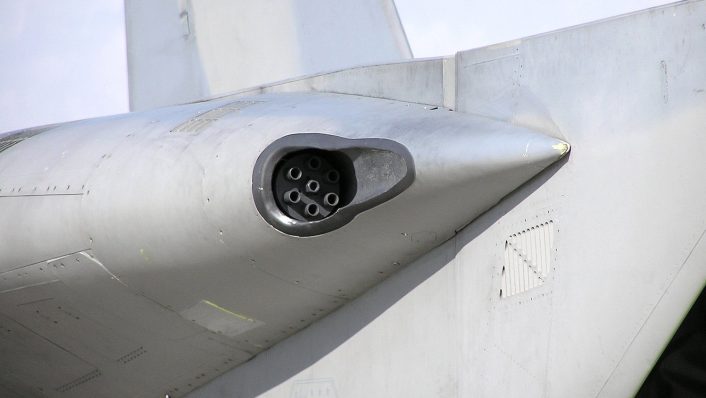
A Easy Resolution to a Complicated Drawback
The jamming concern, attributable to a spot within the ammunition loader, required guide troubleshooting that would take as much as quarter-hour per prevalence, including as much as 798 man-hours yearly. Phrase’s specifically designed 3D-printed insert fills this hole, permitting smoother operations and eliminating the necessity for fixed intervention. The U.S. Air Power estimated that this easy but efficient design might save over 750 man-hours yearly for the forty eighth Fighter Wing.
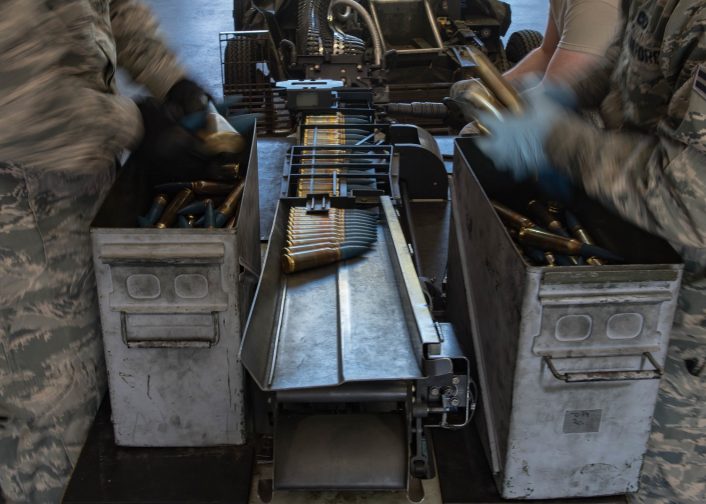
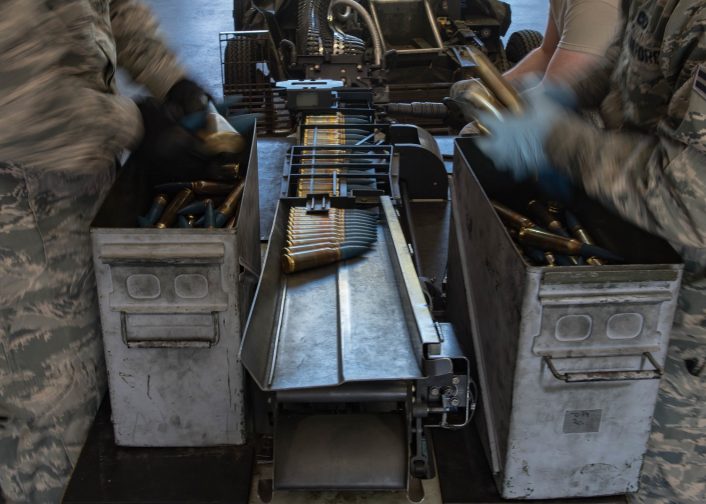
Collaborative Innovation and 3D Printing at Work
Phrase labored alongside Employees Sgt. Bethany Levi, a part of the Air Power Restore Enhancement Program, to conceptualize and design the 3D-printed insert utilizing graphic modeling software program. Over six trials have been performed with 11 prototypes earlier than finalizing the design. The insert is manufactured utilizing a Stratasys F900 3D printer and has now develop into an everyday a part of operations, proving its worth in lowering machine malfunctions and bettering effectivity.
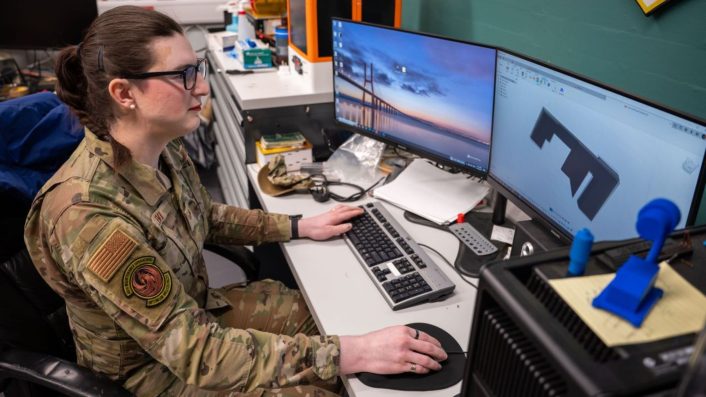
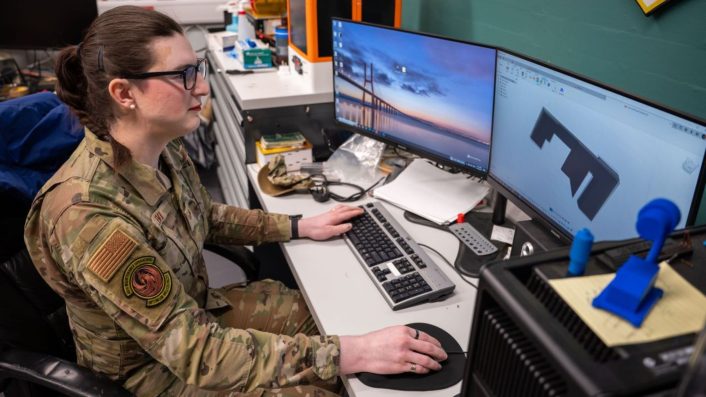
This innovation is a chief instance of how personnel-led concepts can improve logistical operations and enhance gear performance. “Airmen working immediately with gear and processes typically have distinctive insights into operational challenges and potential enhancements,” stated Lt. Col. Jonathan Tolman, forty eighth MUNS commander, praising Phrase’s effort to deal with a standard concern.
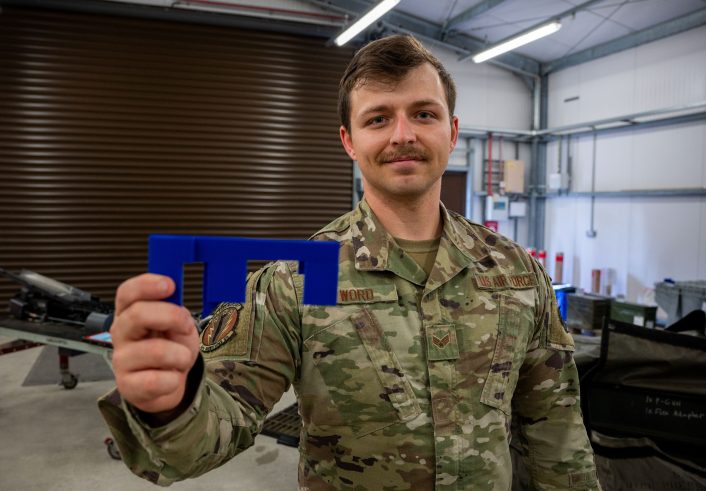
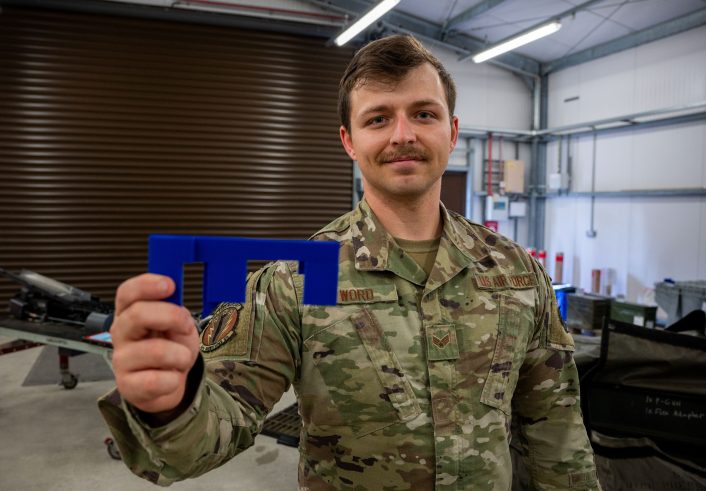
The Position of Additive Manufacturing in Protection
This effort additionally highlights the rising function of additive manufacturing in protection functions. Using 3D printing within the army is increasing quickly, with functions starting from small-scale inserts like Phrase’s innovation to bigger components for techniques such because the M61 Vulcan Gatling gun used throughout U.S. Air Power platforms just like the F-15 and F-22.
Additive manufacturing is changing into an important instrument for the U.S. army, serving to to cut back downtime, enhance readiness, and supply on-demand manufacturing capabilities for vital gear. Phrase’s innovation joins a rising record of 3D-printed options being utilized in army operations, from ammunition loaders to plane repairs.
Wanting Towards the Future
With its success at RAF Lakenheath, the 3D-printed insert is now present process patenting and shall be shared with different U.S. Air Power munitions squadrons. This grassroots innovation is predicted to have a major affect on ammunition dealing with and general operational effectivity throughout the service.
Because the U.S. army continues to embrace 3D printing, the potential for speedy prototyping, quicker repairs, and cheaper options continues to develop. From small inserts to main system parts, additive manufacturing is poised to vary the best way the army approaches gear upkeep and innovation.
Supply: theaviationist.com