Additive Assurance has agreed to combine its in-situ course of monitoring system into Additive Industries’ MetalFab laser powder mattress fusion (LPBF) 3D printers This collaboration seeks to enhance metallic 3D printing course of monitoring in high-value functions.
Because the construct charge and productiveness of metallic 3D printers elevated, in-process monitoring and high quality assurance capabilities are rising in significance.
This know-how performs a crucial function in making certain repeatability, reaching high-reduction yield, and mitigating the danger of wasted materials brought on by failed builds. As such, Additive Industries will now supply stay 3D printer monitoring capabilities to its buyer base.
The corporate’s MetalFab 3D printers will combine Additive Assurance’s AMiRIS high quality inspection system. This unit, which could be mounted instantly onto MetalFab, supplies stay insights into the 3D printing course of. This can reportedly strengthen certification and high quality assurance efforts, enabling shorter manufacturing cycles and better confidence within the last product.
“Our partnership with Additive Assurance aligns completely with our dedication to advancing the capabilities of metallic additive manufacturing,” commented Mark Massey, Additive Industries’s CEO.
“By integrating AMiRIS with our MetalFab portfolio, together with our new MetalFab 300 Flex, we’re enhancing real-time high quality assurance, providing our clients better flexibility, and setting new requirements in manufacturing consistency and reliability.”


MetalFab 3D printers combine in-situ monitoring
Since its founding in 2012, Additive Industries has constructed a considerable portfolio of business LPBF 3D printers. The corporate launched its first system, the MetalFAB1, again in 2016. The 3D printer has since been leveraged by clients in aerospace, automotive, industrial, power, and high-tech market verticals.
Extra just lately, throughout RAPID + TCT 2024, Additive Industries unveiled its latest providing, the MetalFab 300 Flex. This distinctive system options an extendable construct plate that may be accessed by means of a month-to-month or lifetime license. Prospects can lengthen the construct space from 11.81 x 11.81 x 15.75in to 16.54 x 16.54 x 15.75in at any time, to satisfy particular utility wants.
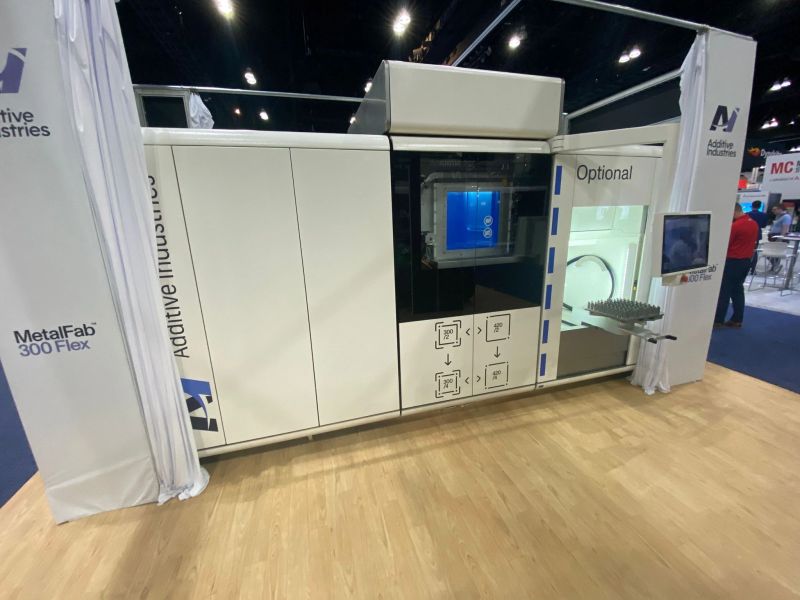
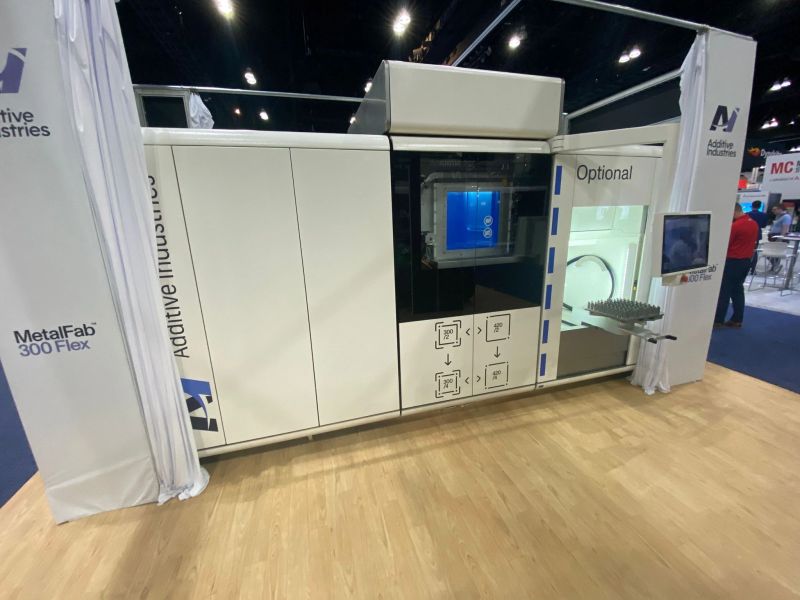
In accordance with the 2 corporations, AMiRIS is a logical extension to the MetalFab sequence of LPBF 3D printers. It is going to reportedly deal with key high quality assurance (QA) challenges confronted in industrial functions reminiscent of house and aerospace manufacturing.
Primarily based in Melbourne, Australia, Additive Assurance launched the beta model of its metallic 3D printing high quality assurance platform in 2019. The corporate launched as a spinout of a mission performed by Monash College and Australia’s Defence Science and Know-how Group.
Its in-situ monitoring unit allows QA reporting throughout a fleet of a number of machine sorts. A patent-pending know-how, it makes use of optical sensors to assemble micron-level element throughout the 3D printing course of. Machine studying is employed to analyse this knowledge, offering insights into the metallic additive manufacturing course of.
AMiRIS is designed to detect varied 3D printing course of instabilities. It options adjustable thresholds for monitoring, notification and intervention to make sure excessive 3D printer utilization and high quality management.
“We’re delighted to be working with Additive Industries so as to add worth to their buyer’s expertise and to push the boundaries of what’s attainable with L-PBF AM,” added Marten Jurg, CEO of Additive Assurance.
The partnership will see broader deployment of in-situ monitoring for MetalFab customers. This, the businesses declare, might result in better adoption of LPBF 3D printing sooner or later.


Defect detection for metallic 3D printing
Defect detection and high quality assurance have rapidly develop into important instruments for metallic 3D printing functions, as producers look to spice up productiveness, guarantee high quality, and scale back waste. This demand has seen extra corporations develop and introduce new course of monitoring choices.
Earlier this yr, Chicago-based 3D printing high quality assurance software program developer Phase3D introduced a collaboration with the United States Air Drive (USAF) and NASA to develop Fringe Analysis. This new in-situ monitoring software program is alleged to be the primary to measure anomalies throughout metallic powder mattress fusion (PBF) 3D printing and correlate these to defects within the last half.
In accordance with Niall O’Dowd, Founder and CEO of Phase3D, the defect-detection software program will improve 3D printer throughput by over 10% yearly. This will likely be achieved by stopping the manufacturing of elements that may later fail inspection. Particularly, the software program is particularly effectively suited to detecting porosity in 3D printed elements. It is a pertinent problem for aerospace functions. Porosity usually causes metallic elements to be rejected by the USAF and NASA.
Elsewhere, 3D printing software program and providers firm Materialise provides its AI-powered Course of Management software program for metallic 3D printing. By this software, customers can analyze knowledge collected throughout 3D printing to regulate the standard of their elements.
This permits faulty elements to be situated earlier than the post-processing and high quality inspection levels, saving customers money and time. In accordance with Materialise, these steps can add 30% to 70% to the prices of a last half.
Wish to assist choose the winners of the 2024 3D Printing Business Awards? Be part of the Professional Committee as we speak.
What does the way forward for 3D printing maintain?
What near-term 3D printing tendencies have been highlighted by business specialists?
Subscribe to the 3D Printing Business e-newsletter to maintain updated with the most recent 3D printing information.
You too can comply with us on Twitter, like our Fb web page, and subscribe to the 3D Printing Business Youtube channel to entry extra unique content material.
Featured picture reveals an AMiRIS unit mounted on a MetalFAB G2 3D printer. Picture by way of Additive Assurance.