In 3D Printing Information Briefs, we’re speaking about PAEK supplies and QA for polymer 3D printing, earlier than transferring on to real-time monitoring of electron beam additive manufacturing. Upwing Power built-in Velo3D’s AM course of for its patented fuel compressor module, decoder-only transformers are producing triangle meshes, and McDonald’s has a 3D printed luminaire. Lastly, in medical information, soundwaves are getting used to harden 3D printed therapies in deep tissue, and after an amputation, an 84-year-old turned the oldest individual on the earth to get a bionic arm from Open Bionics.
Victrex & College of Exeter Renew PAEK Growth Partnership
The College of Exeter and Victrex initially collaborated beginning in 2018 to develop next-gen polyaryletherketone (PAEK) 3D printing supplies, and the partnership was so profitable, they’ve determined to renew it for a further 5 years, and can proceed to take a position collectively in growing PAEK supplies and processes by means of 2028. Victrex is a worldwide chief in PAEK, whereas the college’s Centre for Additive Layer Manufacturing (CALM) is the UK middle of excellence in high-temperature polymer AM, and has loads of high-quality AM tools on-site. Along with the Exeter Applied sciences Group (ETG), that are consultants in high-performance AM polymers, Victrex will work to make clear the science beneath a number of PAEK-related processes, together with AM.
Driving this continued partnership is the work’s potential excessive impression, in addition to strategic alignment with Victrex’s R&D targets. A number of scientific and industrial outcomes have already resulted from their collaboration, together with patents, scientific publications, and case research in regards to the elementary science of PAEK supplies and AM, in addition to new PAEK supplies tailor-made particularly for AM and different new collaborative tasks. Victrex and the college will now proceed to work on funded PAEK analysis tasks with different ecosystem companions, and encourage new proposals for different associated collaborations. Hopefully, the outcomes from their continued work will velocity up improvements by means of digital experimentation and by creating new tailor-made PAEK polymer options.
SKZ & Optris Utilizing Infrared Cameras for 3D Printing QA
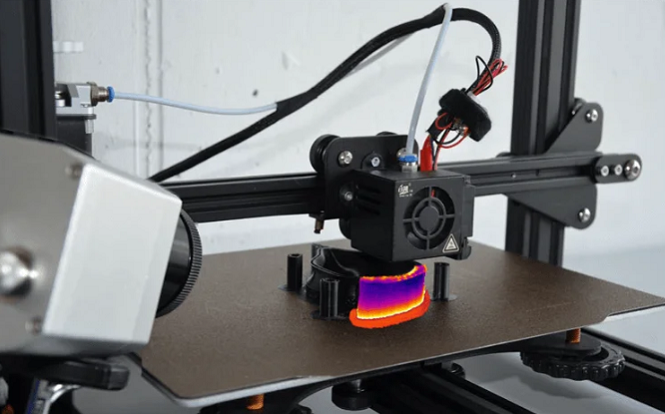
High quality management utilizing the Optris PI 640i throughout 3D printing with the fused filament fabrication methodology (composite picture with IR view and actual picture). Picture Credit score: The German Plastics Heart – SKZ
There are various parameters that must be set to make sure a profitable FFF 3D print, and defects can pop up shortly. Notably when printing spare components with a fast turnaround, these defects must be instantly recognized, so high quality assurance (QA) all through the method and on the completed element is critical in industrial functions. One promising QA method in 3D printing is thermography, as it may be used for complete surfaces and entails no contact. Utilizing an infrared digicam, inspection could be simply performed each throughout and after printing. The German Plastics Heart (SKZ) is partnering with Optris GmbH, which focuses on infrared measurement know-how, to optimize QA in 3D printing with thermal imaging cameras.
Optical monitoring processes are mostly used for 3D printing QA, however they’re not at all times correct. So with the compact, high-resolution Optris PI 640i infrared digicam, SKZ developed a novel imaging choice for inline high quality assurance of 3D printing, utilizing each passive and energetic thermography. The digicam can show filament deposition reside, whereas additionally monitoring course of parameters on the similar time; this permits typical defects like cracks and delamination to be simply recognized. Even throughout picture seize, the thermographic information generated could be analyzed body by body, so you may catch points within the printing course of early. Plus, Optris cameras can examine 3D printed components in a non-destructive approach for harm or performance as soon as they’re in sensible use.
MiniMelt Tracks Electron Beam Powder Mattress Fusion in Actual Time
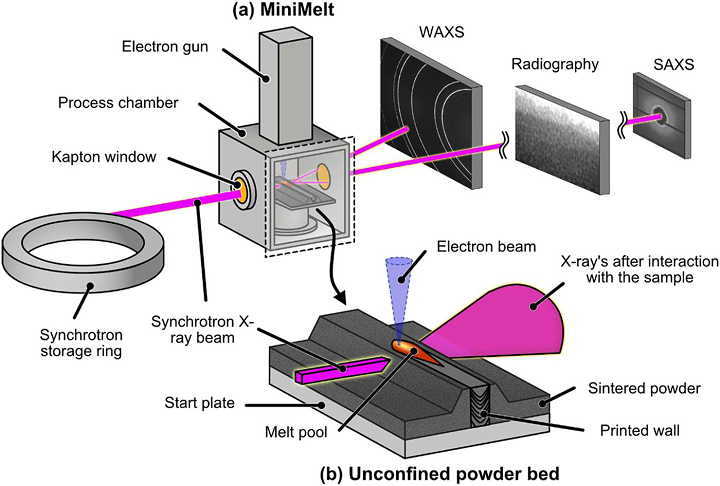
(a) Schematic of the PBF-EB experimental setup (MiniMelt) for measurements of Large-Angle X-ray Scattering (WAXS), radiography, and Small-Angle X-ray Scattering (SAXS) in a synchrotron. (b) Schematic of the unconfined powder mattress the place the x-ray beam interacts with the pattern.
To facilitate alloy and course of improvement for Electron Beam Powder Mattress Fusion (PBF-EB) additive manufacturing, it’s essential to have a strong understanding of the physics of heating, melting, and solidification cycles. Of their paper, a workforce of researchers from KTH Royal Institute of Expertise, Friedrich-Alexander-Universität Erlangen-Nürnberg (FAU), Helmholtz-Zentrum Hereon’s Institute of Supplies Physics, DESY Photon Science, and Freemelt AB clarify how they designed and developed “MiniMelt: An instrument for real-time monitoring of electron beam additive manufacturing utilizing synchrotron x-ray methods.” MiniMelt is a pattern setting for in situ x-ray characterization throughout PBF-EB 3D printing, and the workforce carried out it on the German synchrotron facility PETRA III at Deutsches Elektronen-Synchrotron (DESY). Primarily based on the Freemelt ONE, the MiniMelt has a singular course of chamber that permits for real-time synchrotron measurements throughout printing. The workforce additionally describe a brand new unconfined powder mattress design, which replicates the situations of the PBF-EB course of.
“The primary radiography (15 kHz) and diffraction (1 kHz) measurements of PBF-EB with a hot-work software metal and a Ni-base superalloy, in addition to bulk metallic melting with the CMSX-4 alloy, utilizing the pattern setting are offered. MiniMelt permits time-resolved investigations of the dynamic phenomena going down throughout multi-layer PBF-EB, facilitating course of understanding and improvement of superior course of methods and supplies for PBF-EB,” the researchers wrote.
Upwing Power Integrates Velo3D’s AM for Fuel Compressor Module
Fuel tech innovator and repair firm Upwing Power has efficiently built-in metallic AM into its manufacturing course of, particularly laser powder mattress fusion (LPBF) from Velo3D. Upwing’s patented Subsurface Compressor System (SCS) is used to extend manufacturing and recoverability of pure fuel from wells, and it makes use of a multistage hybrid axial compressor to extend drawdown at consumption and strain at discharge. The compressor’s rotor design particularly requires very advanced floor geometries, however with Velo3D’s metallic AM and experience, Upwing not solely achieves this, however can even transfer from engineering design to full rotor meeting in simply 10 weeks to help nicely deployment schedules. In depth testing with Velo3D proved that the Inconel 718 3D printed components preserve prime quality and sturdiness.
“All of our work at Upwing is underscored by the assumption that steady enchancment is at all times attainable. Our choice to combine additive manufacturing makes us extra scalable and adaptable. It permits us to create components that aren’t solely sturdy, however intricately designed and completed with the best degree of precision,” stated Robert McKeirnan, Vice President of Provide Chain and Exterior Manufacturing at Upwing Power.
Automated Triangle Mesh Era with Decoder-Solely Transformers
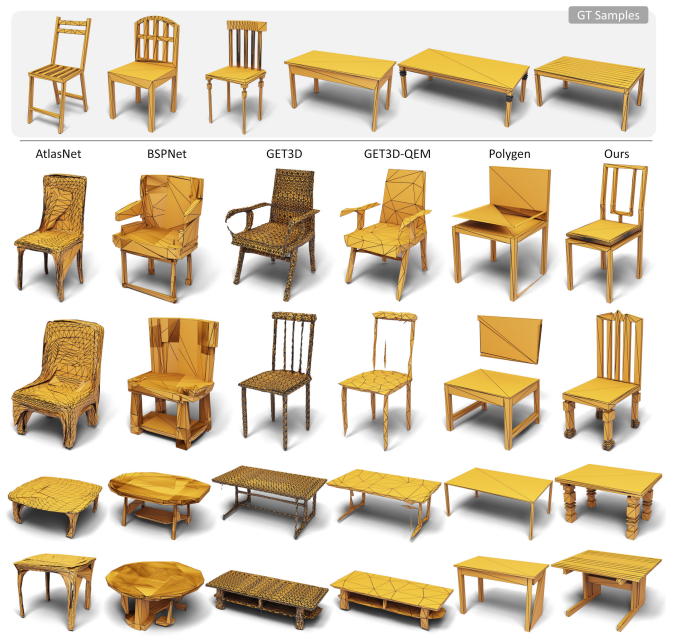
Determine 6. Qualitative comparability of Chair and Desk meshes from ShapeNet (5). Our method produces compact meshes with sharp geometric particulars. In distinction, baselines typically both miss these particulars, produce over-triangulated meshes, or output too simplistic shapes.
Versus various 3D form representations like voxels or level clouds, meshes are simpler to control, extra controllable and compact, match into trendy rendering pipelines, and supply a extra coherent floor illustration. Triangle meshes, particularly, are the primary illustration in pc graphics for 3D geometry. A workforce of researchers from Technical College of Munich, Politecnico di Torino, and AUDI AG wrote a paper on “MeshGPT: Producing Triangle Meshes with Decoder-Solely Transformers,” about automated era of triangle meshes to streamline the method of making 3D belongings. The workforce synthesizes these meshes as sequences of triangles through a direct sequence era methodology.
“We introduce MeshGPT, a brand new method for producing triangle meshes that displays the compactness typical of artist-created meshes, in distinction to dense triangle meshes extracted by iso-surfacing strategies from neural fields. Impressed by current advances in highly effective massive language fashions, we undertake a sequence-based method to autoregressively generate triangle meshes as sequences of triangles. We first study a vocabulary of latent quantized embeddings, utilizing graph convolutions, which inform these embeddings of the native mesh geometry and topology. These embeddings are sequenced and decoded into triangles by a decoder, guaranteeing that they’ll successfully reconstruct the mesh. A transformer is then educated on this discovered vocabulary to foretell the index of the following embedding given earlier embeddings. As soon as educated, our mannequin could be autoregressively sampled to generate new triangle meshes, instantly producing compact meshes with sharp edges, extra intently imitating the environment friendly triangulation patterns of human-crafted meshes. MeshGPT demonstrates a notable enchancment over cutting-edge mesh era strategies, with a 9% enhance in form protection and a 30-point enhancement in FID scores throughout varied classes,” they wrote of their summary.
Cooper Lighting Options 3D Prints Customized Gentle for McDonald’s
McDonald’s Corp. wanted pendant designs for brand spanking new shops, however an off-the-shelf design was not possible—they wished a scalable resolution, brief lead time, aggressive price, and to personal the IP rights. The corporate labored with Cooper Lighting Options, which was acquired by Signify in 2020, to design a 3D printed, semispherical luminaire with an embossed sample. In the course of the session and design course of, the shopper and designers had a number of conversations, and Cooper Lighting had a 3D printed pattern product prepared in three months. After three extra months of hashing out the small print, McDonald’s gave its last approval for the {custom} luminaire, which Signify’s Phillips Lighting workforce printed out of a polycarbonate materials custom-built for its merchandise. The fixture’s floor has raised patterns and contours to form the sunshine, and the luminaire is sturdy, simple to scrub, recyclable, and doesn’t yellow with age, which have been all elements McDonald’s wished. Plus, as a result of Signify has 3D printing services everywhere in the world, native manufacturing is feasible.
“The entire fixture is completed in a single print; it doesn’t cease, there aren’t any breaks, the printing simply slows down a bit of, thickens up the polycarbonate, and creates that line in order that gentle doesn’t penetrate,” defined Lawrence Fallon, Enterprise Growth Supervisor, Prentalux, Cooper Lighting Options. “It was one thing McDonald’s had by no means seen in a position to be accomplished on a single-piece fixture. A number of producers may’ve added paint, or they may’ve added a basket over it or hung one thing over a glass fixture to create that sort of look, however the truth that we have been in a position to print it proper into the fixture was very distinctive.”
Ultrasound Waves Harden 3D Printed Remedies in Deep Tissues
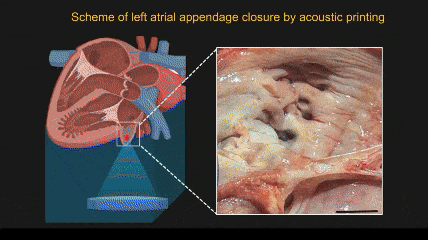
The printing technique of DVAP can shut the left atrial appendage inside minutes. The thermal picture exhibits the temperature rise throughout the printing. Picture credit score: Junjie Yao, Duke College; Shrike Yu Zhang, Harvard Medical Faculty.
Through the years, researchers developed a photo-sensitive ink for medical 3D printing that responds on to focused beams of sunshine, hardening shortly into the ultimate construction. However, researchers can solely use clear inks, which limits biomedical functions, as gentle can’t attain previous just some millimeters into tissue. Now, engineers at Duke College and Harvard Medical Faculty have created a biocompatible ink that solidifies into completely different biologically suitable 3D shapes and constructions when it’s uncovered to and absorbs ultrasound waves. Plus, because it responds to sound waves and never gentle, the viscous ink can be utilized in deep tissues for biomedical functions together with bone therapeutic and coronary heart valve restore. The strategy known as deep-penetrating acoustic volumetric printing, or DVAP, and begins with a sonicated ink, or sono-ink, manufactured from hydrogels, microparticles, and molecules designed to react to ultrasound waves. As soon as it’s delivered, a particular printing probe sends ultrasound waves into the ink, which hardens parts into constructions. The workforce efficiently performed three assessments as a proof-of-concept of their new DVAP methodology.
“DVAP depends on the sono-thermal impact, which happens when soundwaves are absorbed and enhance the temperature to harden our ink. Ultrasound waves can penetrate greater than 100 occasions deeper than gentle whereas nonetheless spatially confined, so we are able to attain tissues, bones and organs with excessive spatial precision that haven’t been reachable with light-based printing strategies,” defined Junjie Yao, affiliate professor of biomedical engineering at Duke, who designed the ultrasound printing know-how for DVAP.
“As a result of we are able to print by means of tissue, it permits for lots of potential functions in surgical procedure and remedy that historically contain very invasive and disruptive strategies. This work opens up an thrilling new avenue within the 3D printing world, and we’re excited to discover the potential of this software collectively.”
Grandmother Turns into World’s Oldest Individual to Get a Bionic Hero Arm
84-year-old Christa Seubert from Würzburg, Germany is the oldest individual on the earth to be fitted with a 3D printed bionic Hero Arm from Open Bionics. After first pondering she had a blocked carpal tunnel, it turned clear that Seubert had an aggressive most cancers. Chemotherapy failed, and her proper arm was amputated to avoid wasting her life. However she’s very energetic and enjoys gardening, biking, crafting, and strolling her canine, and located it onerous to get again to doing on a regular basis actions, like buttering bread, on her personal. She wanted a light-weight prosthesis, and inside one hour of becoming, Seubert was in a position to make use of her new Hero Arm to stroll her canine. Open Bionics, based in 2014, works to develop reasonably priced, assistive gadgets that may assist flip disabilities into superpowers. Its Hero Arm makes use of myoelectric sensors to detect the underlying muscular contractions generated from the arm’s particular muscle teams, and amplifies and converts them to proportional, intuitive bionic hand actions. 3D scanning and printing make sure that every bionic arm is personalized for its consumer.
“For Christa, being fitted with a Hero Arm has massive benefits. It’s the convenience of use, the very low weight in comparison with different prosthetic fittings, and the convenience of placing on and taking off that I feel will enable her to get pleasure from her independence,” stated Mathias Stegemann, CPO at APT Prothesen in Würzburg, who fitted Seubert for her bionic arm.
Subscribe to Our E mail E-newsletter
Keep up-to-date on all the most recent information from the 3D printing trade and obtain data and provides from third occasion distributors.